There are more and more companies being formed every day with one goal in mind: to reach into space. These companies are founded on technology and precision, with nearly everything they create needing “can’t fail” quality in both design as well as execution. This is a story about one such WAZER customer.
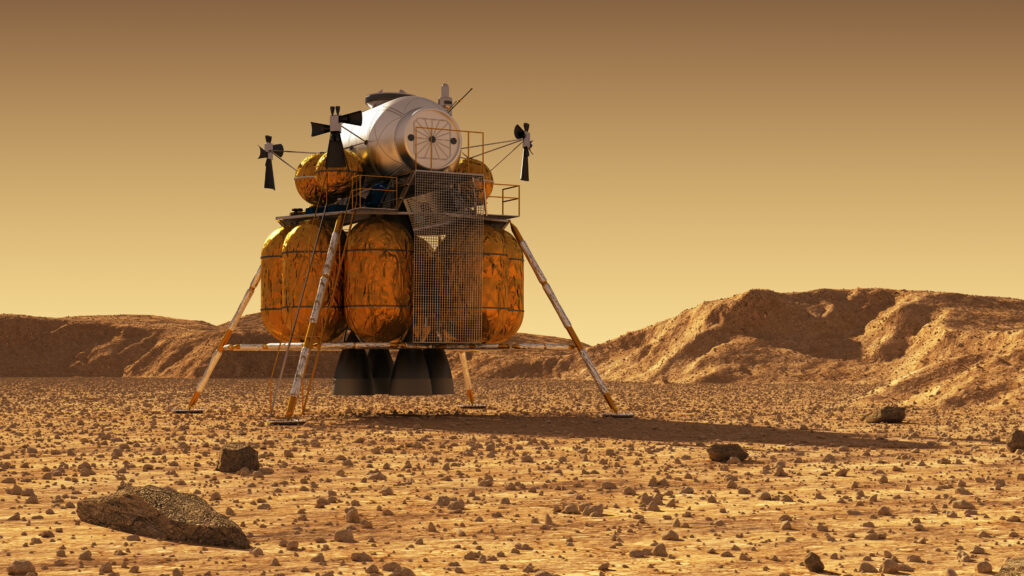
Space exploration has stringent guidelines for construction and operation, which has a direct impact on design considerations for every one of these builds. With demanding production timelines and the need for risk proofing their designs, multiple iterations must be accomplished in a timely fashion without compromising budgets.
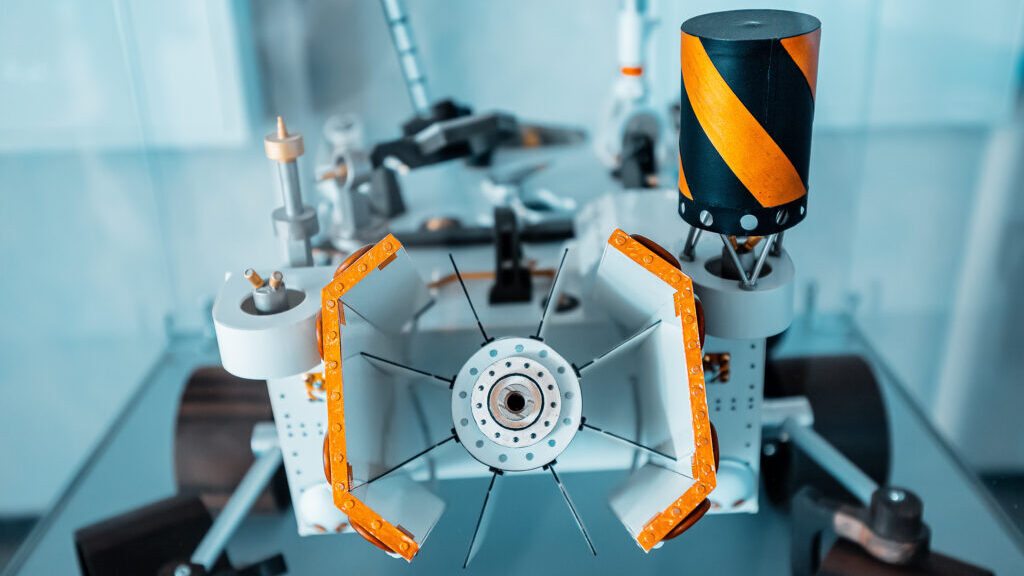
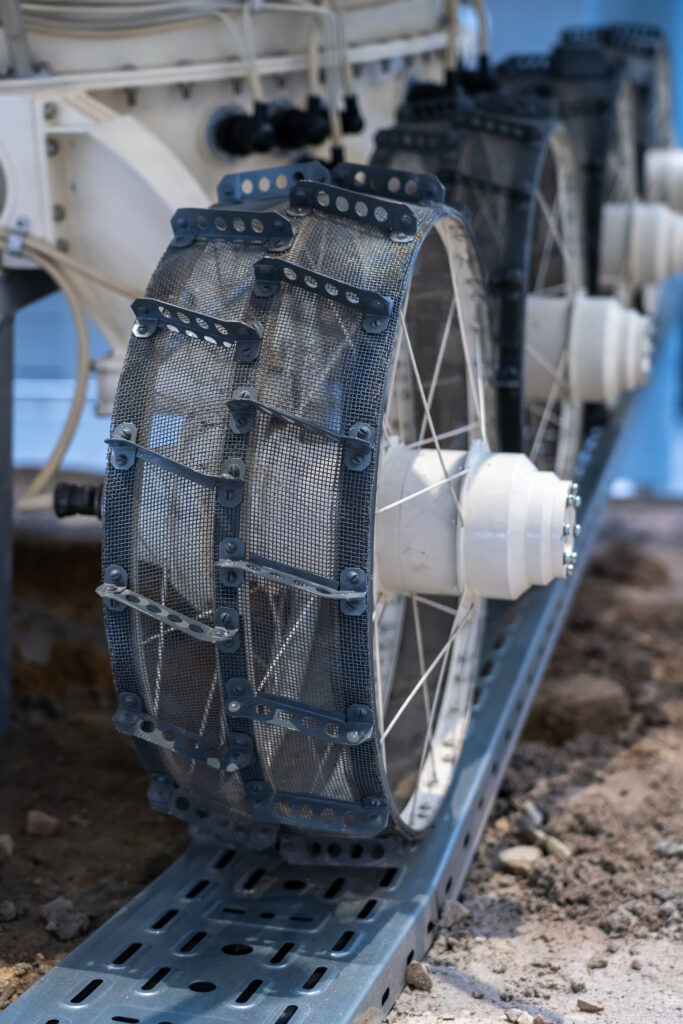
Our WAZER customer summed up their company: “we are a lean, nextgen tech company that is based on efficiency of process.” He added, “we need to quickly make parts without supply chain issues or spending time getting competitive quotes.”
WAZER cuts any material, from titanium to stainless steel or composites
He also said the WAZER facilitates their lean production process and shorter cycle times because it is well-designed, offers plug-and-play operation, and anyone can use it with little or no training. The WAZER’s ability to cut any material without expensive tooling is also put to the test, as it is used to create parts in aluminum, titanium, stainless steel, and various composites and polymers. He also felt “we’re able to meet tight deadlines due to the versatility of the WAZER.”
“Using it saves the cost of another WAZER every few months”
He also noted how economical the WAZER turned out to be, “the machine paid for itself in just 2 or 3 months”, adding “it saves the cost of another WAZER every few months.” During peak usage, the WAZER is working several days per week turning out dozens of precision parts destined for space, and even more that are used in support or testing roles on the ground.