Founded in 1965, Primex Plastics has grown exponentially to become one of the largest plastic sheet extruders in the United States. Primex delivers state-of-the-art plastic solutions, and is the only company that owns the entire production process from compounding materials and colorings, to custom extrusions and distribution, giving their global partners exceptional flexibility, options, and value.
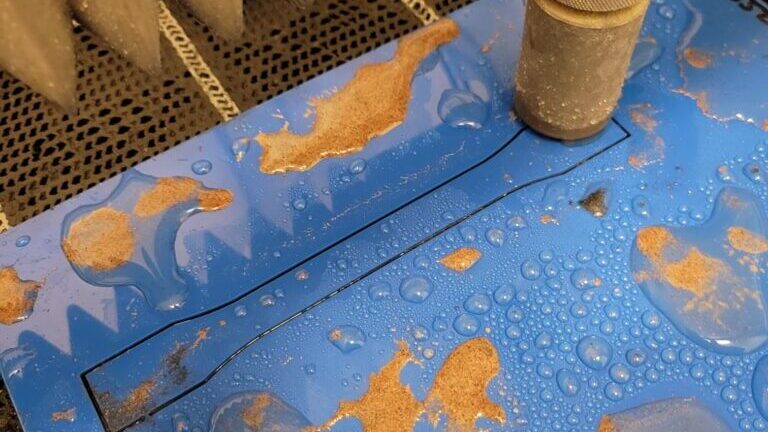
Matt Vandivier, a 30-year veteran of the company who handles materials testing, spoke of the large amount of trial work that goes into creating new materials, new blends, and new formulations prior to their being offered for sale. He also described the labor intensive and time consuming process to generate the “dogbone” samples for testing plastic materials, a process using jigs and fixtures that “often took longer to produce samples for testing than it did to test them.” The poor edge quality of these sample pieces could also skew test data on occasion.
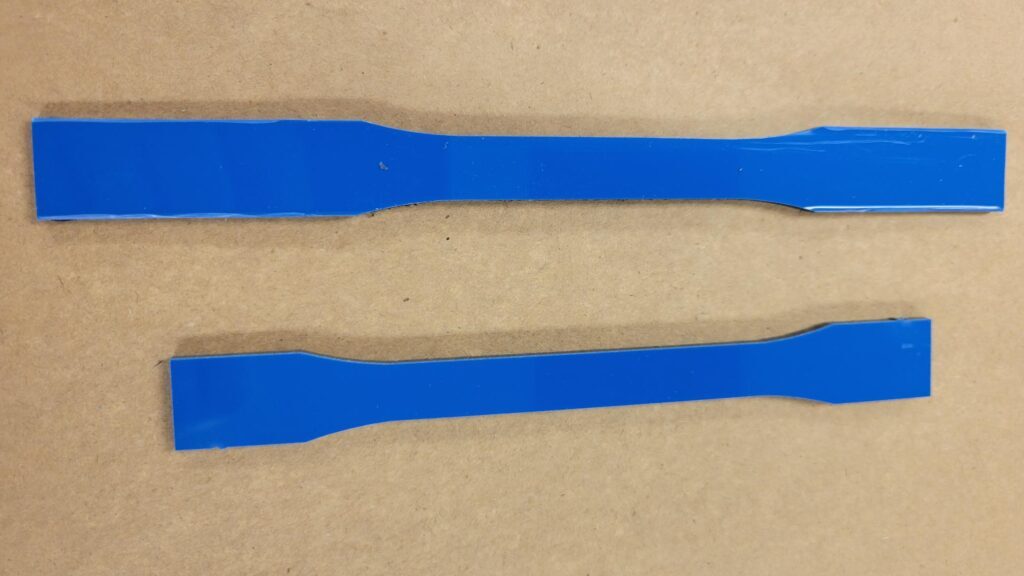
In 2020, the company turned to the WAZER to help modernize the production of test samples, and the improvement was immediate. The test samples can now be quickly and accurately cut to a variety of geometries to meet ASTM and ISO specifications for elongation, flexural modulus, Izod impact, Taber abrasion, and more, and the clean edges ensure clean data. The WAZER’s “cold process” waterjet cutting also doesn’t introduce heat into the samples that could alter their physical characteristics or produce noxious fumes like a laser could.
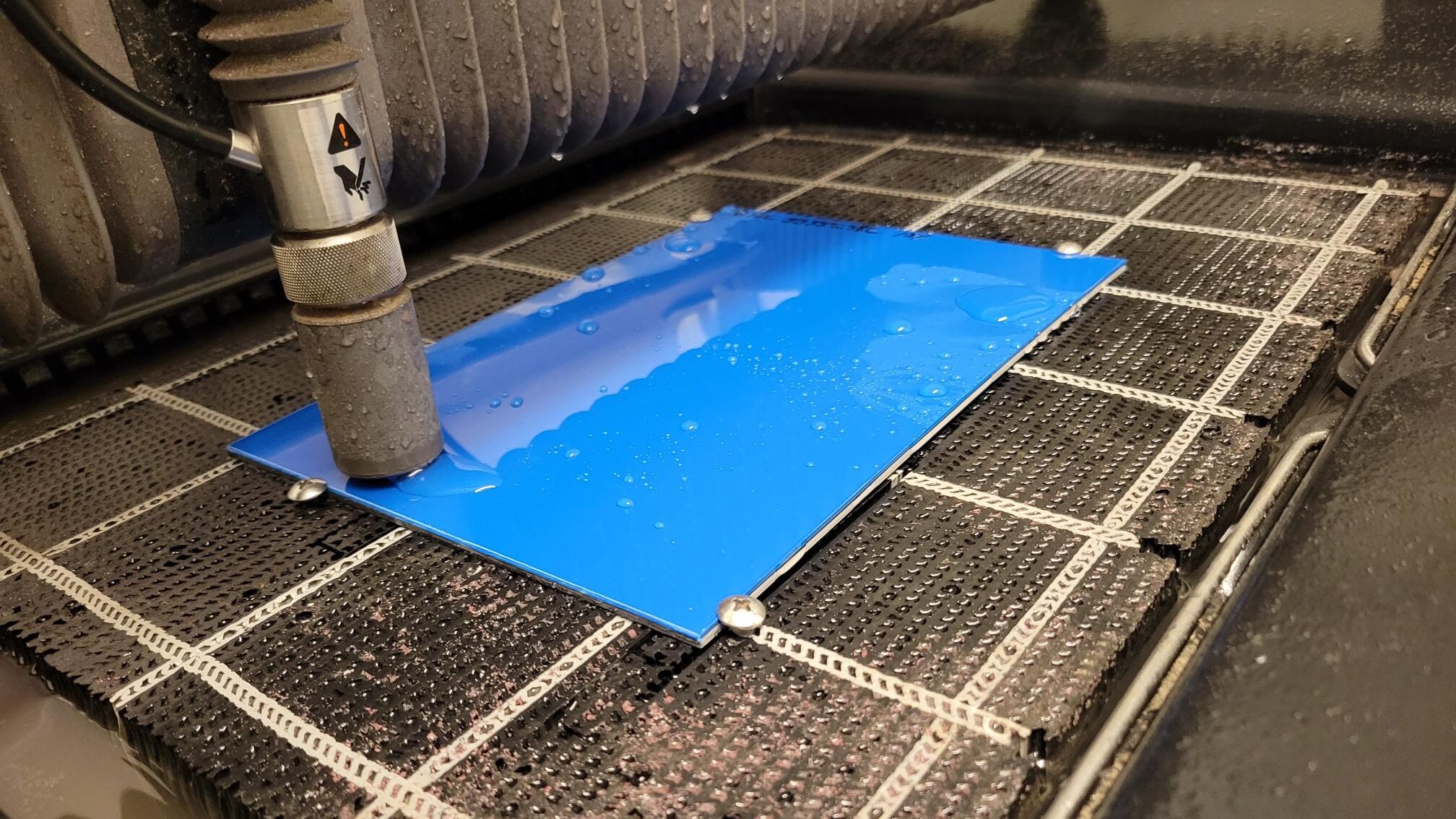
“For what it costs, it’s a no brainer”
The WAZER increased the quality of the test samples, and the accompanying data quality. Its affordability and small footprint were well-suited to the lab environment. Matt described how bringing in-house materials testing which was previously outsourced by their UK factory actually paid for the WAZER, adding “for what it costs, it’s a no brainer.” He also spoke of the efficiency and ease of use, adding “I can cut samples on the WAZER while I do other things.”