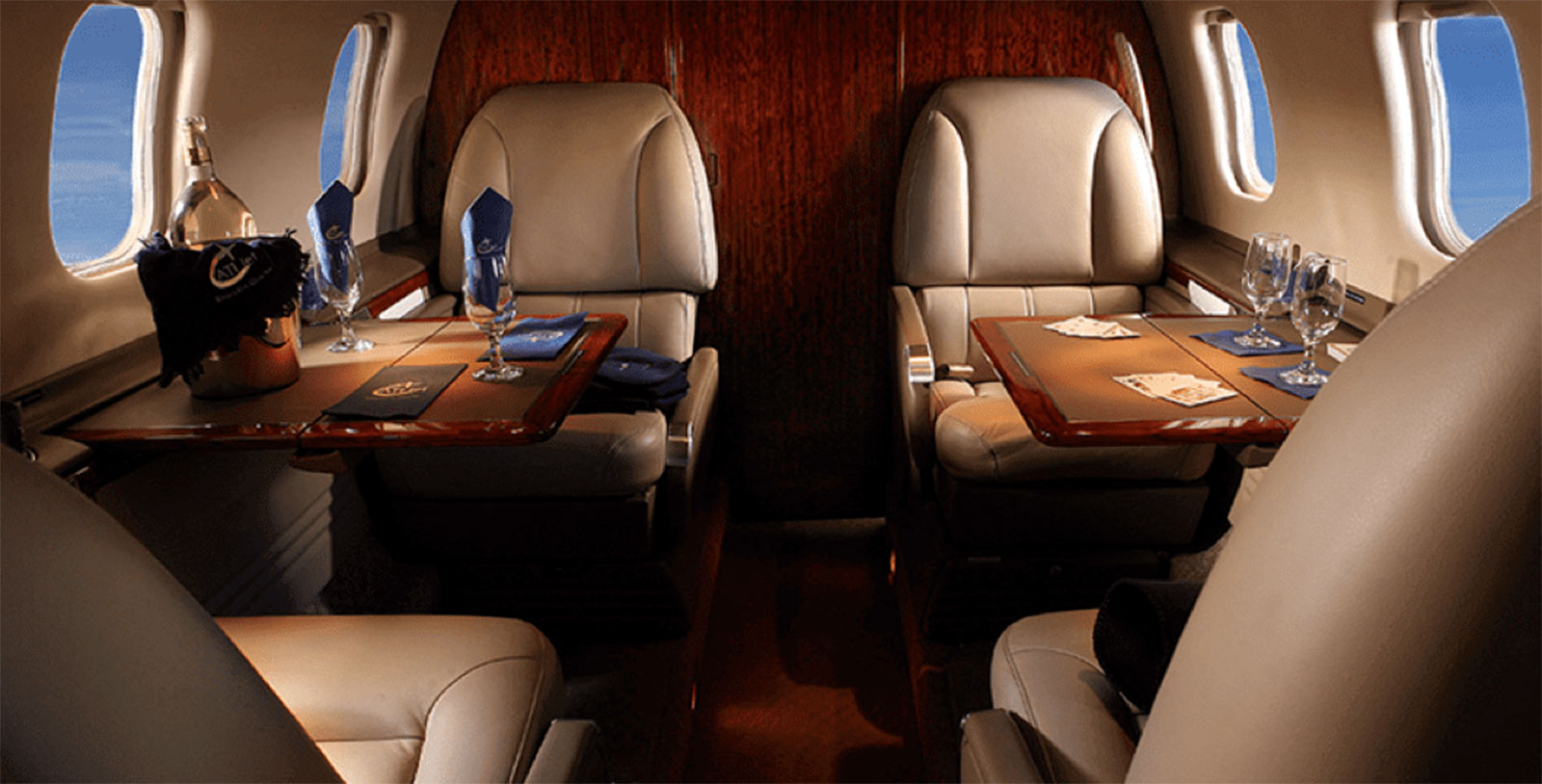
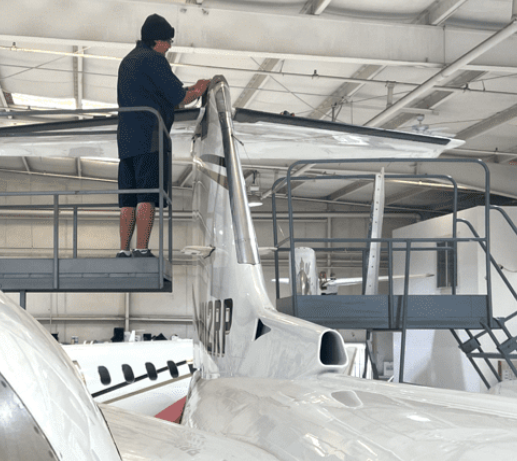
A leading private aviation provider tells how they use their WAZER waterjet cutter to help upgrade their flight experience. They have flown a fleet of Lear Jets for over 30 years, serving passengers with safety, luxury, and state of the art technology, because their private aviation customers are highly demanding and expect a first class flight experience at every stage of their journey.
Being in a competitive luxury business requires continuously upgrading their fleet, adding or improving features and services to differentiate their planes and flight experience. Working on these planes means working mostly in aluminum (with some stainless steel), often designing and creating new parts to add specialized features into existing aircraft.
Jay, Director of Flight Safety, leads the work to upgrade and enhance the fleet. Previously, he designed prototypes utilizing parts that were produced with CNC Punch machines, made by hand, or outsourced to fabrication shops-which often had long lead times. The result was poor quality, unnecessary delays, and inconsistency from part to part.
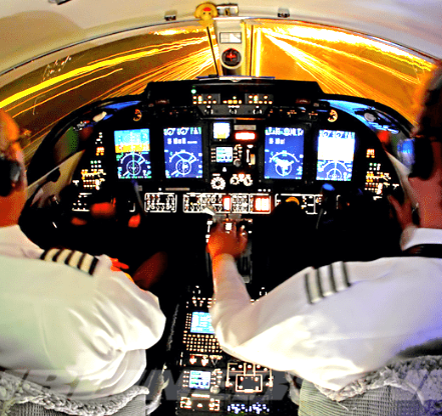
In order to support the entire fleet, and maintain the quality they are known for, Jay brought in a WAZER small waterjet for aviation use, keeping the work in house, improving quality, and increasing speed to part. It paid off on one of their biggest projects, to install modern WIFI across the fleet, which required retrofitting the planes with bracketry and electronics boxes to house the equipment. An alternate supplier’s competing parts were so large that they would have filled one-third of the baggage compartment. Instead, Jay’s team designed their own, and fabricated it on the WAZER, saving weeks of time, as well as keeping the baggage compartment intact.
“It’s incredible how accurate it is.”
Working with the WAZER helps speed the process of designing and prototyping new parts for existing aircraft. Jay noted that with the WAZER, if he needs to revise a part to move a screw hole or a mounting tab, he can do it in-house and cut new parts without delay. In a side-by-side test, he cut a new part in 3/8” aluminum in 10 minutes, while the same piece cut by hand took 2 hours.