Tight-Tolerance Sheet Metal Cutting:
Custom Knife Making With a Waterjet
In a company full of EDC (Everyday Carry) enthusiasts, building a folding pocket knife was only a matter of time. Nearly every WAZER engineer carries a pocket knife or some other type of multitool on their person at all times, including me, so custom tailoring a knife to meet my needs was an obvious project to pursue. However, pocket knives are precise tools needing tight tolerances in order to ensure a solid lockup and smooth action. I knew I could easily achieve this with common post-processing techniques, but just how precise could the WAZER be with no extra help? To answer this question I was challenged to make one pocket knife using any post-processing techniques needed, and the other with no post-processing at all. Waterjets typically leave behind a slight draft angle when cutting (depending on the cut rate of the machine) due to how the material is eroded by the abrasive and high pressure water. My task was to figure out what cut rate was needed to produce the minimal amount of draft on my parts.

CNC Milling Versus Waterjet Cutting
Most pocket knives are produced using CNC milling machines, which can easily create counterbores and other features that do not require cutting through the entire thickness of the material. The downside of conventional machining is the setup complexity: it requires advanced fixturing methods and a careful toolpath-generation process. Waterjets, while easy to set up and program, have to cut all the way through the thickness of the material. So in order to achieve features like counterbores, my design included layers of thin sheet material with varying geometry. Even though this requires more assembly, it allows for more creativity with skeletonizing the knife and creating otherwise impossible features between layers, like the brass inlay in the middle layer of the scales. WAZER has the ability to cut complex profiles in very tough materials like titanium and knife steel with minimal setup.
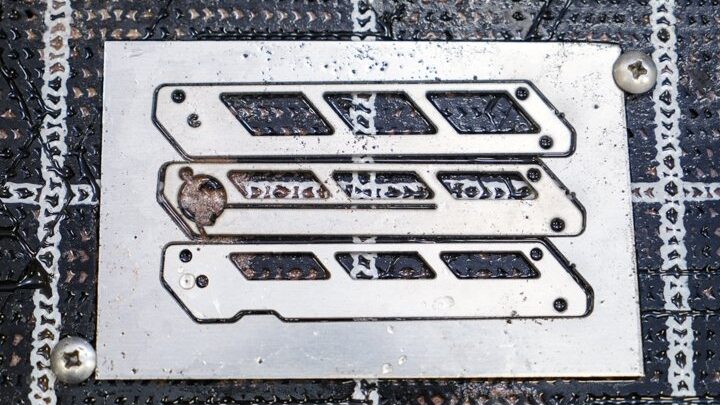
Cutting and Assembling a Custom Knife
I chose titanium with brass inlays for the knife’s frame and M390 stainless steel for the blade. Due to titanium’s toughness, the draft angle was quite steep when using the rough cut speed. This didn’t matter as the blade was sanded and then ground to achieve the final finish. In order to perfectly size the holes for the knife pivot and pins, a reamer was used in the pierced holes made on the WAZER.
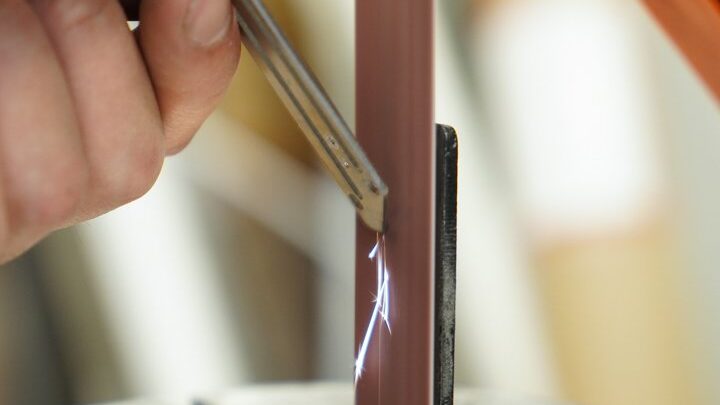
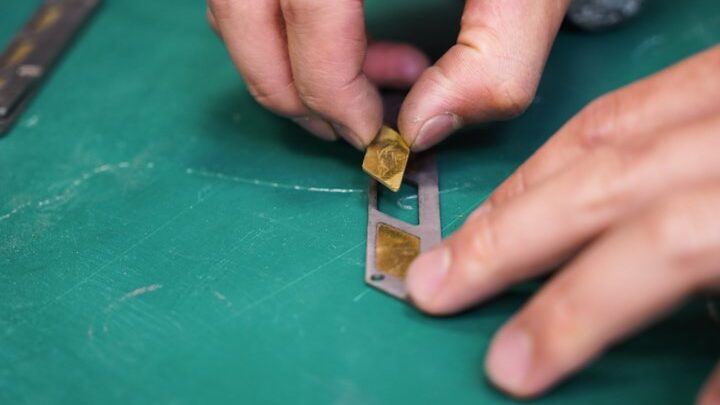
The brass inlay pieces were hammered into place, using draft angles to my advantage so the brass pieces wedged into their titanium enclosure. Once all pieces were assembled together, the draft angles along the edges of the frame were ground down using a coarse grit sanding belt to achieve a uniform look along all the edges. Countersinks were drilled to make room for the flathead screws used to hold all the pieces together.
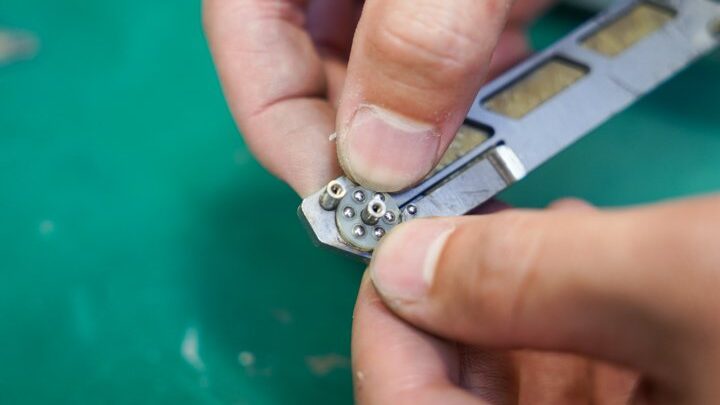
Cutting Aluminum Instead of Titanium
After the first knife was complete, cut rate testing began for the second knife, which would use no post-processing. The goal of the project was to make two identical knives with different techniques, but it soon became obvious that the toughness of the titanium would prevent us from achieving a zero-degree draft angle (i.e. 90 degree edges) no matter how slowly we ran the waterjet. For this reason, we decided to switch from titanium to aluminum, a much softer and easier-to-machine material. By cutting out small squares in a test piece of aluminum, I dialed in an ideal cut rate that would minimize the draft angle.
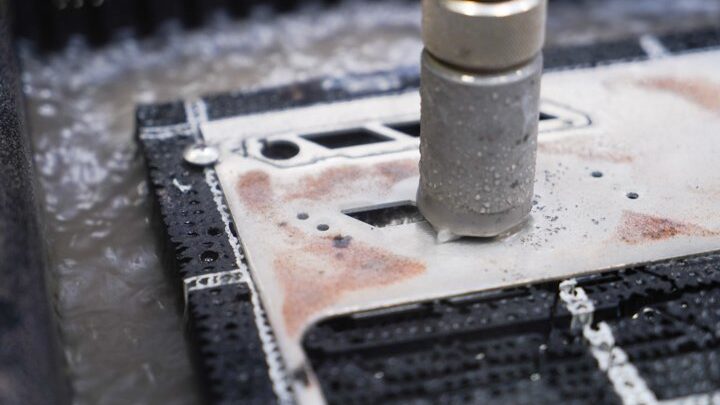
Sometimes Hand-Finishing Is Faster Than CNC Cutting
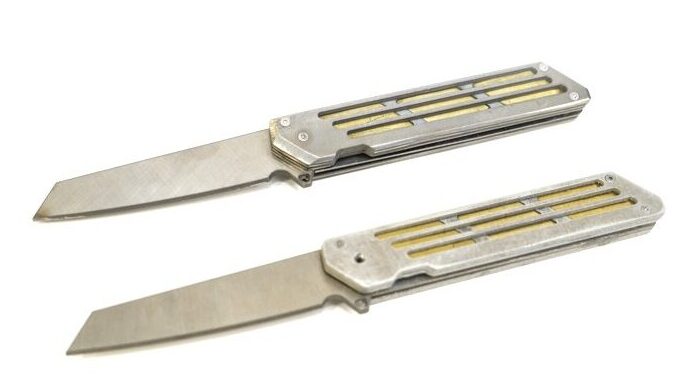
Although CNC Machines are capable of amazing precision, there are some tasks that are better left to traditional post-processing techniques. Even though assembly of the second knife was extremely easy and painless, the small fitment issues and the long cutting time drastically outweighed the benefits.
The first knife was quick to cut and straightforward to complete. The second knife took many hours to dial in the correct feed rate and many more hours of cutting due to the slow feed rate, even though it is made of aluminum, a material that is generally extremely quick to cut. Just because it is possible to cut zero-draft parts on WAZER, it’s not always worth it since some edge-finishing can be done faster with hand tools.